The section of aluminum extrusion is divided into three categories:
Solid section: low product cost, low mold cost
Semi hollow section: the mold is easy to wear and tear and break, with high product cost and mold cost
Hollow section: high product cost and mold cost, the highest mold cost for porous products
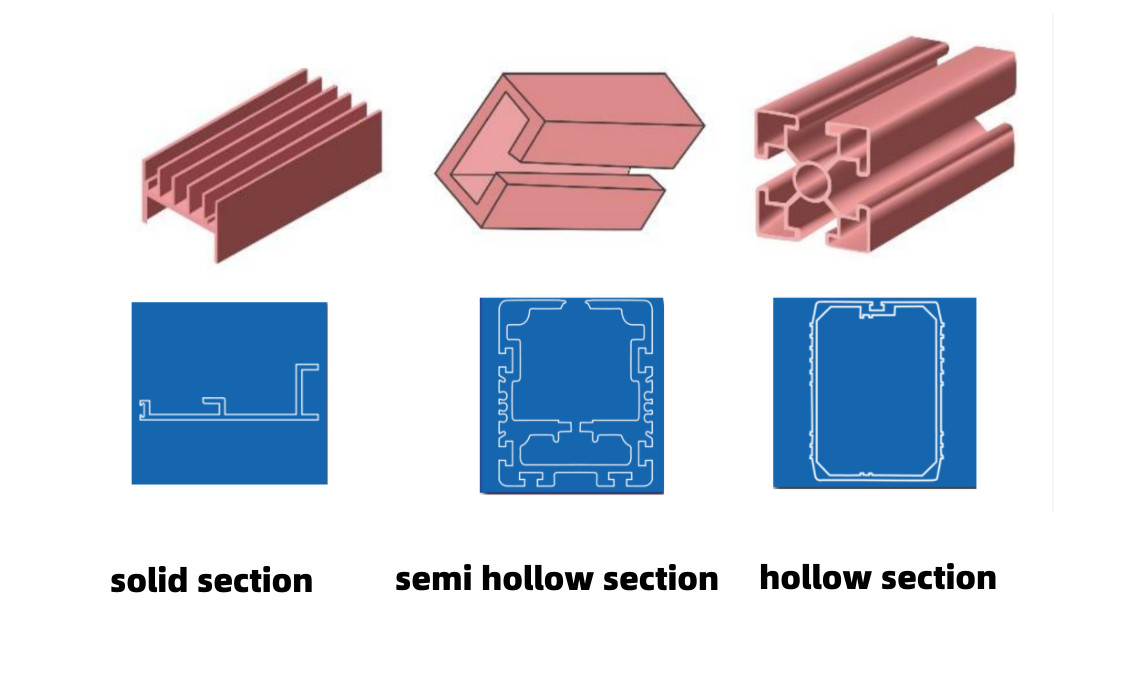
1.Avoid asymmetrical and unbalanced sections
Asymmetric and unbalanced sections increase the complexity of extrusion, and at the same time, quality problems are prone to occur, like the dimensional accuracy and flatness are difficult to ensure, the bowing and twisting of parts, low production efficiency, and molds are easy to wear and tear during mass production.
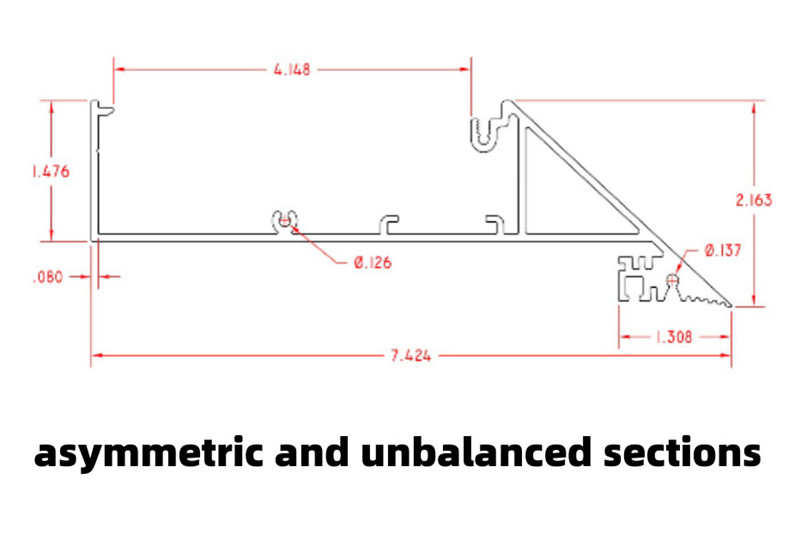
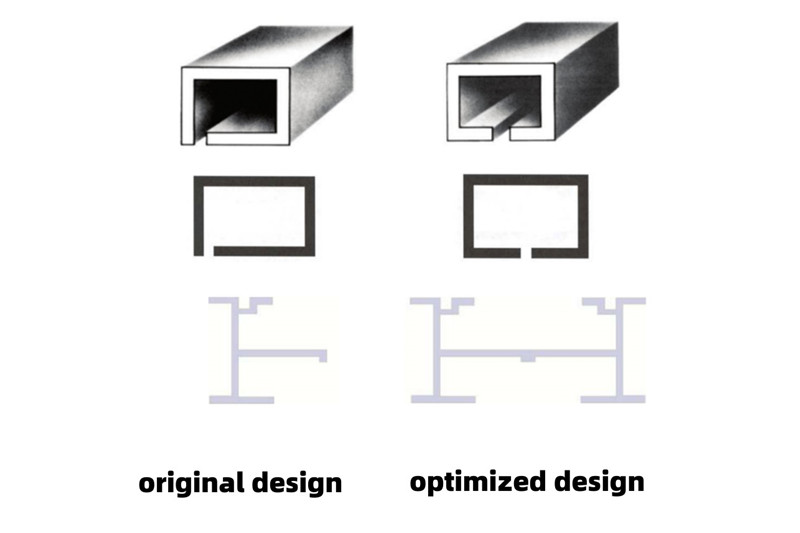
The more asymmetric or unbalanced of the aluminum extrusion section, the more difficult it is to ensure straightness, angle and other dimensional accuracy.
Although asymmetrical and unbalanced shapes can be produced, metal is less likely to flow into narrow and irregular areas during extrusion, where distortion or other quality issues can easily occur.
Also, even if it is possible to extrude asymmetric and unbalanced shapes, higher tooling costs and higher production costs due to slower extrusion speeds, eventually lead to higher mold processing costs and production costs.
The greater the number of sides and channels in an extrusion profile, the less accurate and more expensive it will be.
2.The simpler the sectional shape, the better
Some product design engineers design too many features in an aluminum extrusion. Although the unique advantage of aluminum extrusions is to add holes, slots or screw bosses in the section, it will lead to very complicated mold design, or not extrudable at all with very expensive production costs.
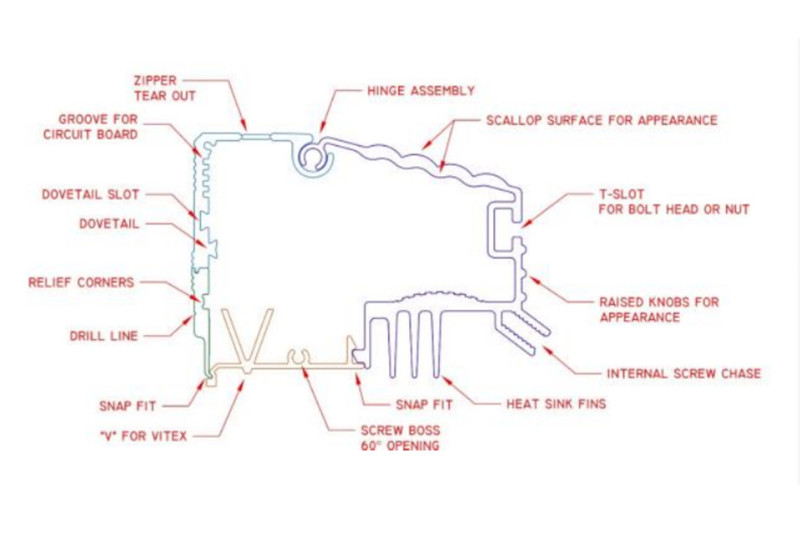
When the section of the extrusion is too complex, it can be considered to use two or more parts for extrusion.
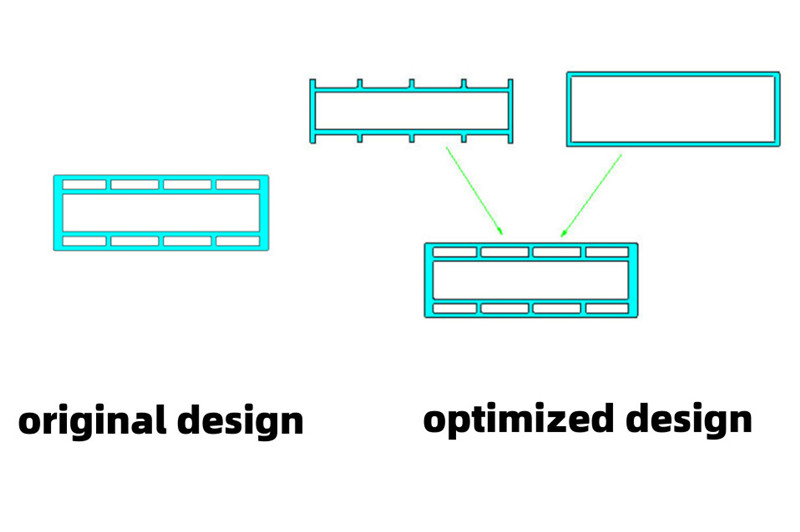
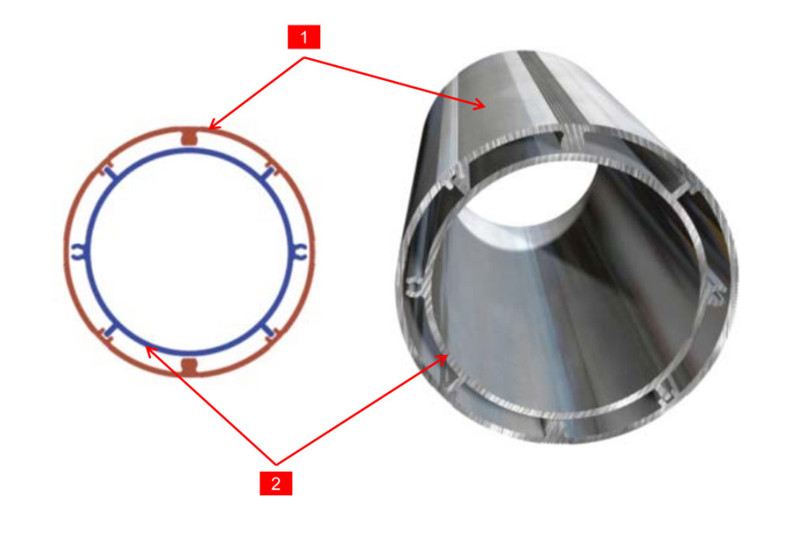
3.Porous hollow section optimized to single-hole hollow section
By optimizing the porous hollow section into a single-hole hollow section, the mold structure can be simplified and the cost can be saved.
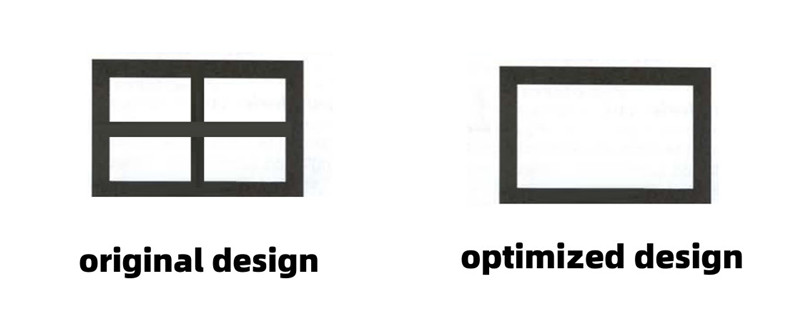
4.Hollow section optimized to semi-hollow section
By optimizing the hollow section to a semi-hollow section, the mold structure can be simplified and the cost can be saved.
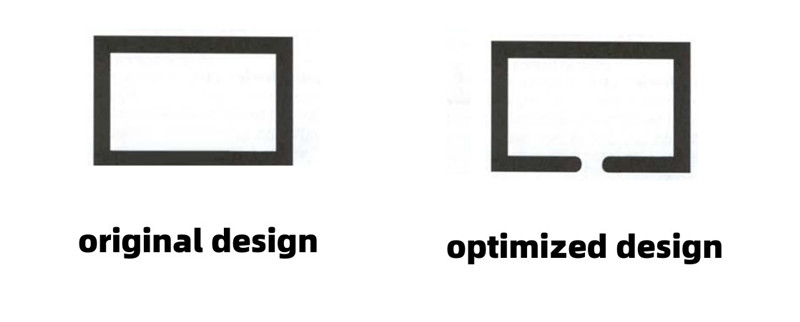
5.Semi-hollow section optimized to solid section
By optimizing the semi-hollow section to a solid section, the mold structure can be simplified and the cost can be saved.
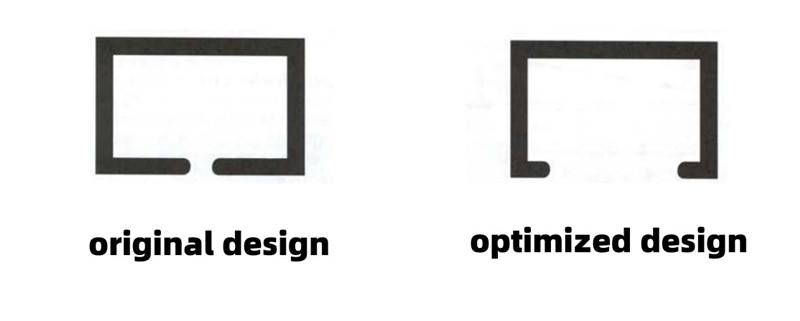
6.Avoid porous section
Porous sections can be optimized through design to reduce mold costs and difficulty in processing and production.
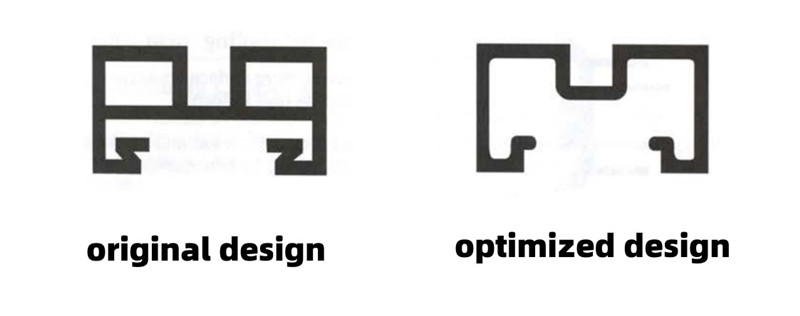
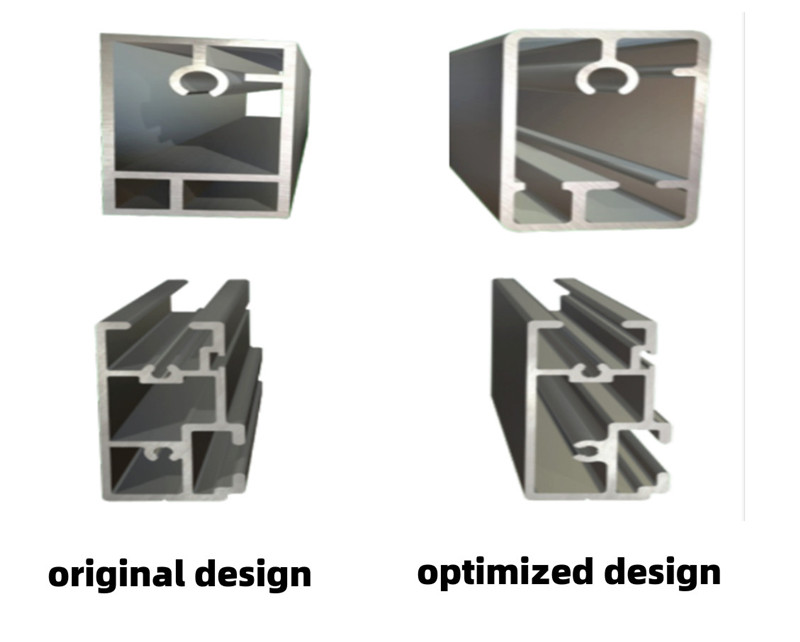
Edited by May Jiang from MAT Aluminum
Jan. 16, 2023
Post time: Feb-18-2023