Aluminum casting is a method for producing high tolerance and high quality parts by pouring molten aluminum into a precisely designed and precision engineered die, mold, or form. It is an efficient process for the production of complex, intricate, detailed parts that exactly match the specifications of the original design.
The Aluminum Casting Process
1.Permanent Mold Casting
Much of the expense of aluminum permanent mold casting is the machining and shaping of the mold, which is normally made from gray iron or steel. The mold is shaped into the geometric shape of the designed part with the specifications and shape of the part divided into two halves. In the injection process, the halves of the mold are tightly sealed such that no air or contaminants are present. The mold is heated prior to the pouring of the molten aluminum, which can be ladled, poured, or injected.
At the completion of the process, the mold is allowed to cool to allow the aluminum part to solidify. Once cooled, the part is rapidly removed from the mold to prevent the formation of defects.
Regardless of how simple the process may seem, it is a scientifically and technically engineered method for producing high volume parts.
2.Sand Casting
The sand casting process involves packing sand around a reusable pattern that has the shape, details, and configuration of the final product. Included in the pattern are risers that allow the molten metal to be poured into the mold and for hot aluminum to feed the casting during solidification to prevent shrinkage porosity.
Included in the pattern is a sprue that allows molten metal to be inserted into the mold. The dimensions of the pattern are slightly larger than the product to account for shrinkage during the cooling process. The sand has the weight and strength to maintain the shape of the pattern and is resistant to interacting with the molten metal.
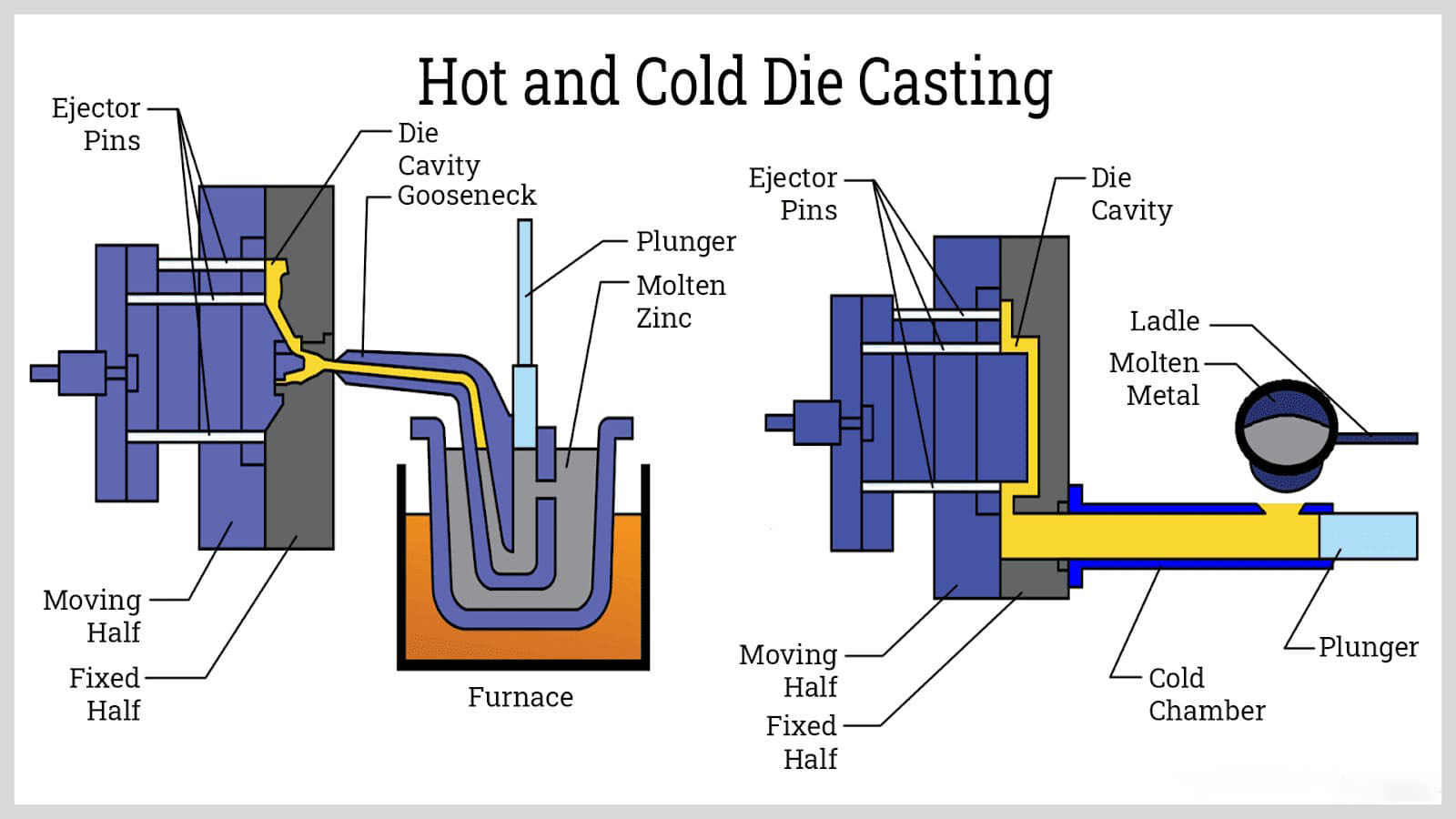
Vacuum die casting uses an airtight bell housing that has a sprue opening at the bottom and a vacuum outlet at the top. The process begins by submerging the sprue below the surface of the molten aluminum. A vacuum is created in the receiver creating a pressure differential between the die cavity and the molten aluminum in the crucible.
The pressure differential causes the molten aluminum to flow up the sprue into the die cavity, where the molten aluminum solidifies. The die is removed from the receiver, opened, and the part is ejected.
Controlling the vacuum and the pressure differential between the die cavity and molten aluminum makes it possible to control the fill rate required by part design and gating requirements. Control of the fill rate enhances the ability to determine the soundness of the finished part.
Having the sprue submerged below the surface of the molten aluminum ensures that the molten aluminum will be the purest alloy free from oxides and dross. Parts are clean and sound with minimal foreign materials.
5.Investment Casting
Investment casting, also known as lost wax casting, begins with wax being injected into the die to create the pattern of the finished product. The waxed patterns are attached to a sprue to form a tree ike configuration. The tree is dipped into a slurry multiple times, which forms a strong ceramic shell around the wax shape.
Once the ceramic has set and hardened, it is heated in an autoclave to complete the dewax burnout. To achieve desirable temperature of the shell, it is preheated before being filled with the molten aluminum, which is poured into the sprue and passes through the series of runners and gates into the molds. When the parts harden, the ceramic is knocked off leaving the tree connected parts to be cut from the tree.
6.Lost Foam Casting
The lost foam casting process is another type of investment casting where wax is replaced with polystyrene foam. The pattern is molded from polystyrene in a cluster assembly like the runner and sprues of investment casting. Polystyrene beads are injected into heated aluminum molds at low pressure with steam added to expand the polystyrene to fill the cavities.
The pattern is placed in densely packed dry sand that is vibration compacted to eliminate voids or air pockets. As the molten aluminum is poured into the sand mold, the foam is burned off, and the casting is formed.
Common Applications Of Casting Aluminum
Because of its excellent physical and chemical properties, many major industries use cast aluminum. Here are a few common applications of the material.
1. Medical Industry
Medical part manufacturers rely on aluminum casts for their strength and lightweight in making prosthetics, surgical trays, etc. Aside from that, the process is suitable for making complex and accurate shapes which the industry is known for. Also, aluminum is the right material due to its corrosion resistance since much medical equipment comes in contact with body fluids.
2. Automotive industry
Automotive parts manufacturers rely on aluminum casts for their lightweight properties without comprising strength and durability. As a result, it has improved fuel efficiency. Furthermore, making automotive parts with complex shapes with the aluminum casting process is easier. Aluminum casts are suitable for making parts such as brakes and steering wheels.
3. Culinary Industry
Cast aluminum is useful in the culinary industry because of its durability, corrosion resistance, lightweight, and excellent heat conduction. Aside from that, the material is suitable for making cookware because of its excellent heat dissipation, i.e., it can heat up and cools down quickly.
4. Aircraft Industry
Aluminum parts are perfect for the aircraft industry due to their lightweight and strength. Its light weight allows an aircraft to use less fuel to carry more weight.
Source:
https://www.iqsdirectory.com/articles/die-casting/aluminum-casting.html
https://waykenrm.com/blogs/cast-aluminum/#Common-Applications-of-Casting-Aluminum
Edited by May Jiang from MAT Aluminum
Post time: Jul-26-2023